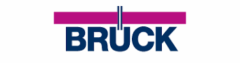
Essai robotisé sensible par ultrasons
DÉFI #1
Est-il possible de conduire une personne à ultrasons avec un robot?
DÉFI #2
Quelle est l’incidence du milieu de couplage sur la sensibilité?
DÉFI #3
Dans quelle mesure les géométries inconnues peuvent-elles être détectées à l’aide de la tête d’essai?
À propos du projet
Finalités
Dans le cadre de ce projet, il a été examiné si un robot pouvait s’acquitter des tâches qui avaient été accomplies jusqu’à présent — plus précisément: l’essai par ultrasons de grands éléments de forgeage. L’objectif était de déterminer si un robot pouvait porter la tête ultrasonique avec précision et avec une force d’extrusion fiable.
Trois questions importantes devraient être abordées afin d’évaluer la faisabilité technique et les avantages potentiels d’un processus d’audit robotisé.
Le robot peut-il conduire la tête ultrasonique de manière sensible?
La tête d’essai doit être déplacée avec une force d’extrusion constante le long d’une voie donnée afin d’obtenir de bons résultats de mesure et de reproductibilité des résultats d’essai. Pour ce faire, le robot doit être contrôlé de manière à assurer une liaison optimale entre la tête d’essai et la pièce forgée.
Quelle est l’influence du «moyen de couplage» sur la sensibilité du système?
Étant donné que le dispositif de couplage joue un rôle essentiel dans la transmission du signal dans le processus d’essai par ultrasons, il est examiné dans quelle mesure le milieu de couplage influence l’utilisation sensibilisante de la tête ultrasonique par le robot. L’objectif est de démontrer la capacité du système robotisé en cas d’adhérence afin d’obtenir un résultat reproductible (effort de contact constant, vitesse de déplacement constante).
Dans quelle mesure le robot peut-il réagir aux différentes formes d’objets forgés?
Étant donné que les éléments de forge peuvent varier sous leur forme, on teste dans quelle mesure la planification et la commande du robot peuvent être adaptées aux différentes géométries des pièces d’usine. À cette fin, une combinaison de planification ferroviaire basée sur la CAO (planification ferroviaire hors ligne) et d’étalonnage de la pièce à usine réelle sera utilisée pour évaluer la faisabilité d’une adaptation automatisée de la géométrie.
Il s’agit également d’étudier les autres avantages de la numérisation de l’ensemble du processus d’audit, par exemple en ce qui concerne l’amélioration de la documentation ou l’évaluation ultérieure.
DESCRIPTION DE L’ENTREPRISE
Fabian Bonner
Direction de l’équipe d’assurance qualité Brück GmbH
Situation actuelle
Une procédure d’examen existante a été examinée avec la société Brück GmbH à Ensheim. Il s’agit de très grandes pièces forgées d’un diamètre inférieur ou égal à 6,5 mètres. Jusqu’à présent, les membres du personnel ont dû conduire la tête ultrasonique à la main, ce qui constitue un travail pénible et inergonomique. Étant donné que la taille de l’élément de forge exige que la tête d’essai soit répétée manuellement, le temps nécessaire au cours du processus d’essai s’accroît.
Avec l’augmentation des demandes sur le marché, le stockage et la documentation des données de mesure sont confrontés à de nouveaux défis. Jusqu’à présent, les résultats de l’audit n’ont pas été systématiquement enregistrés sous forme numérique.
Il convient donc d’examiner s’il est possible d’automatiser et de numériser le processus par un robot.
Étapes à suivre
Tout d’abord, le processus manuel précédent a fait l’objet d’une analyse approfondie afin d’identifier les spécificités et les défis individuels. Sur cette base, un concept d’automatisation a ensuite été mis au point pour décrire la manière dont le robot peut s’acquitter de cette tâche.
L’accent a été mis sur la garantie d’un guidage précis et rigoureux de la tête d’épreuve à ultrasons, ainsi que sur l’enregistrement et la documentation numériques des données d’essai.
L’un des principaux outils a été la conception initiale du mouvement d’essai sur la base de données de conception (CAD). Étant donné que chaque composant peut être fabriqué de manière légèrement différente en raison d’écarts naturels de fabrication, un étalonnage a également été effectué sur la pièce usagée. Cela a permis d’adapter la planification ferroviaire à la géométrie réelle et d’améliorer la précision du processus.
L’un des points les plus importants de l’essai par ultrasons était que le robot fonctionne avec une «commande active». Cela signifie qu’il conduit la tête d’essai à une pression régulière. Cela a également permis d’obtenir des résultats de mesure homogènes et cohérents sur des surfaces plus étendues, ce qui a permis d’accroître la reproductibilité des résultats des essais.
L’application du produit de couplage a également été examinée de manière plus approfondie: Quelle peut être l’épaisseur? Dans quelle mesure doit-il être réparti de manière équitable? Il était important de reconnaître l’incidence de l’épaisseur du liant sur le réglage de la force afin de développer une stratégie d’application optimale.
Au cours d’une phase d’essai finale, le processus d’essai nouvellement automatisé a été testé à l’aide d’une géométrie et de paramètres de procédé exemplaires, avec la conclusion que la solution robotisée est au moins équivalente au processus d’essai manuel. En particulier dans les conditions limites d’une répétabilité complète, les solutions sont comparables.
Résultat du projet
Le projet a montré: L’automatisation du processus d’essai par ultrasons à l’aide d’un robot délicat est techniquement possible et présente de nombreux avantages.
Les mesures restent fiables et homogènes, car le robot conduit la tête d’essai à pression constante. Le processus est devenu moins contraignant pour le personnel, en réduisant le travail manuel pénible sur le plan physique. En outre, la solution offre la possibilité d’enregistrer toutes les données d’essai par voie numérique et de les stocker pour chaque composant. Cela améliore la traçabilité et optimise l’assurance de la qualité.
L’utilisation est également rentable sur le plan économique, étant donné que l’automatisation permet de réduire les temps d’essai et, partant, de réduire les coûts. Dans l’ensemble, le projet fournit une base solide pour le déploiement à grande échelle de ce processus d’essai automatisé dans l’industrie.